Back to Don's Maps
Back to Tools of the Stone Age Index
Stones were able to be transformed directly into tools by shaping. The first such tools were called choppers and chopping tools.
The first step consists of detaching a flake from the stone with aid of a hammerstone, generally another pebble.
By repeating this gesture, they had a rough edge.
Photo: Kathy King 2010
Source: Display at Musée d'archéologie nationale, Saint-Germain-en-Laye
A cast of a Solutrean "laurel leaf" spear point, over 13 inches long. These delicate and beautiful implements were prepared by delicate flaking across the surface. Many are so large and delicate that they could never have been actually used, and may have been status objects.
Photo: Man before history by John Waechter
The Neanderthal Levallois technique
Photo: Don Hitchcock 2008
Source: Display at le musée de l'Homme de Néandertal, La Chapelle-aux-Saints
These are high quality facsimiles demonstrating the Levallois Technique.
The Levallois technique, invented 300 000 years ago, was a revolutionary technique. The knapper prepared a core of flint to get a shape commonly known as a tortoise shell, which presents a convex surface. From a few blows, one or more flakes, of pre determined shape can be detached from the nucleus. The standardised flakes can then be altered for various purposes. The Levallois technique produced many successive flakes, four on average, from the same prepared nucleus, which allowed the knapper to economise on good quality flint.
Photo: Kathy King 2010
Source: Display at Musée d'archéologie nationale, Saint-Germain-en-Laye
Levallois nucleus/core from the region of Bergerac.
This is superb quality flint, worked by a master craftsman.
Photo: Don Hitchcock 2015
Catalog: 2006.17.16.1
Source: Original, Musée d'Aquitaine à Bordeaux
Mousterian biface hand axe, made of flint. This is an important piece from the Department Vienne near Châtellerault (La Belle Indienne), as may be seen from the inscription on the axe.
Length 172 mm, width 126 mm, thickness 27 mm.
This handaxe is seen by many collectors as the non-plus-ultra for the Moustérien de tradition acheuléenne (MTA) bifaces.
Note that at the time of writing the catalog of the museum is in error regarding its origin, ascribing it to Fontmaure (Vienne). My thanks to Katzman of http://www.aggsbach.de/ for the heads up about this important discrepancy. See http://www.aggsbach.de/2016/10/the-ordinary-and-the-special-triangular-handaxes-bifaces/
Katzman writes (p.c.) that about 2006 an American collector bought a similar piece at a French auction house for $14 000 USD.
Photo: Don Hitchcock 2015
Additional text and access to Bordes (1979): Katzman of http://www.aggsbach.de/
Catalog: 60.1563.1
Source: Original, Musée d'Aquitaine à Bordeaux
These are the drawings of the piece above by Bordes from his text Typologie du Paleolithique ancien et moyen, 1979.
Photo: Bordes (1979)
Mousterian biface hand axe, Les Morines (Sauveterre-de-Guyenne, Dordogne).
Photo: Don Hitchcock 2015
Source: Original, Musée d'Aquitaine à Bordeaux
Making Flint Tools
![]() |
Shaped flakesVariously shaped flakes may be struck off fine-grained rocks by varying the angle and force of the blow and using different hammers. The principle is simple: radiating waves of force, like ripples in a pond, crack out chips. Telltale signs exist on flakes which have been produced by man; they never occur on naturally broken stones. |
![]() |
Baton techniqueA 'soft' baton (or retouchoir, retoucher) of wood or antler or bone is used to strike the core, initiating a fracture which detaches a flake from the core. This is often a very roughly shaped piece of bone or antler, with the only indication that it was used as a tool being the damage caused to the surface by the edge of the tool being shaped. |
Acheulian hand-axeAn Acheulian hand-axe shows the effects of delicate edge retouching by the baton method. With this technique, toolmakers fashioned especially sharp, straight-edged cutting tools. |
![]() |
![]() |
Pressure FlakingUsing a pointed implement of wood, bone or stone, the artisan forces a flat flake from the lower surface of the tool by pressing against the edge in a slightly downward movement. |
Shouldered PointEnd-on views of pressure-flaking show how force is applied to the tool edge itself. Controlled fracturing with this method results in finer flakes and finer tools, like the leaf point at right. |
![]() |
Techniques improve as man evolves
About 150 000 years ago, the first of several dramatic advances in tool technology took place. With their increasing brain capacities, early homo sapiens acquired the foresight and ability to perceive in a raw lump of stone a finished tool of a complex nature. To produce such implements required long series of preparatory steps, but with new methods, developed from the old techniques of percussion and, later, pressure flaking, early men produced tools of increasing sharpness, delicacy and beauty.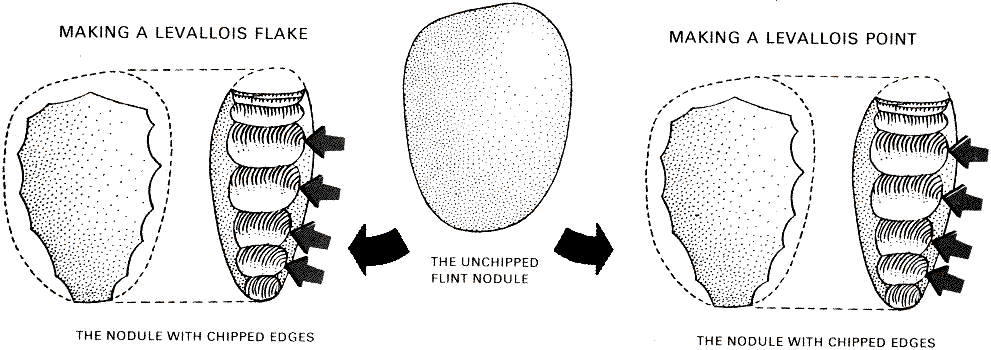
![]() |
Making a Levallois FlakeThe levallois flake has a distinctive predetermined shape. A nodule is prepared by trimming its sides (top). This core is further refined by flaking small chips from both surfaces (center). A final brisk blow at one end removes the finished flake (bottom), already sharp and in need of no further retouching. |
Making a Levallois PointThe levallois point is begun in exactly the same way, except that in the second stage, instead of chipping the top surface, the maker drives off two large parallel flakes (middle), leaving a ridge down the center. A light blow then removes a small flake from one end; one final blow drives off the point.(I think the object of the small flake being taken off is to make sure that a reasonably wide end is left on the point. This small preliminary flake leaves two stronger ridges leading up to the main ridge, so that the point starts wide then tapers to a point - Don) |
![]() |
The Levallois (Mousterian) technique animation for a blade (left) and a point (right).
Click on the images to expand and view the animation of how the techniques are performed.
Photo: José-Manuel Benito Álvarez
Permission: licensed under the Creative Commons Attribution-Share Alike 2.5 Generic license.
Blade Core Technique
![]() |
A core for many blades is prepared by breaking a large flint nodule in two with a hammerstone. Using either piece, the maker then knocks long, thin flakes from the outside rim leaving a tapering fluted core. From this he produces a whole series of finished blades, striking them off one by one as he spirals around the nucleus. By striking between ridges he will get a hollowed blade (top right). It has been estimated that a two-pound nucleus, flaked in this fashion, will yield some 25 yards of working edge, whereas a hand-axe shaped from the same stone would yield about four inches of effective edge. |
Making a Burin from a blade
![]() |
Starting with a fluted blade, the toolmaker first snaps the pointed end (left). Next, using a wood or antler hammer, he chips the broken end to make a striking platform, then dulls one edge (two views, second drawing). He may now make either a single or double beveled edge (third and fourth drawings) with one of the methods described in detail below. |
![]() |
Tipping a burin can be done in two ways. In the first, the blade is rested on an anvil stone and struck with a wood or bone baton, causing the tip to fly off at an angle determined by how the blade is held. In the second method, the blade is pressed sharply against a stone to remove the tip. If a double bevel is desired, the blade is turned over and flaked again.
|
A classic burin
Diagrammatic angle burin of one Cape Denbigh type and detached spall.
Arrows designate points of burin blow.
Note negative bulb (below arrow and on spall).
Photo and text:
Giddings (1956)
Burin spalls often turn up in an archaeological context. They were sometimes used as tools in their own right.
These are from Le Souci, Lalinde, Collection Delugin, Iegs 1923
Photo: Don Hitchcock 2014
Source: Musée d’art et d’archéologie du Périgord, Périgueux
References
- Bordes F., 1979: Typologie du Paleolithique ancien et moyen, Paris: Editions du Centre national de la recherche scientifique.
- Giddings J., 1956: The Burin Spall Artifact, ARCTIC, [S.l.], p. 229-237, jan. 1956. ISSN 1923-1245.